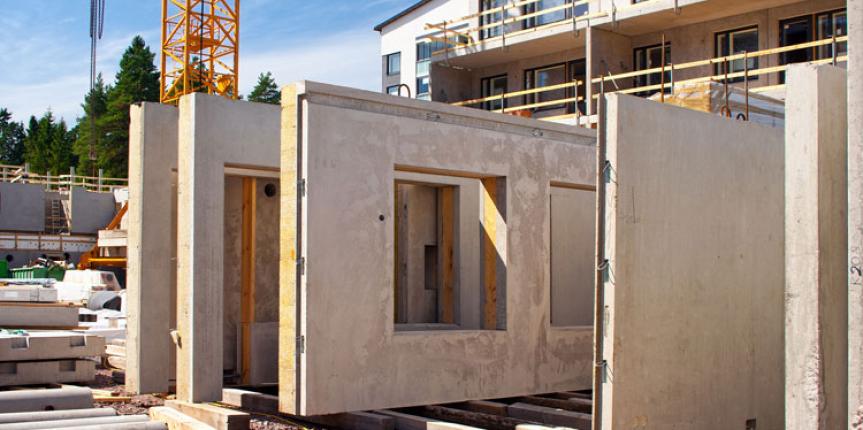
Precast concrete may be a construction product created by casting concrete in a very reusable mold or “form” that is then cured in a very controlled setting, transported to the development web site and upraised into place (“tilt-up”). In distinction, standard concrete is poured into website-specific forms and cured on site.
Precast stone is distinguished from formed concrete employing a fine combination within the mixture, that the final product approaches the looks of present rock or stone. A lot of recently dilated polystyrene is getting used because of the cores to formed wall panels. This can be light-weight and has higher thermal insulation.
Precast is employed inside exterior and interior walls. By manufacturing formed concrete in a very controlled setting (typically noted as a formed plant), this concrete is afforded the chance to cure and be closely monitored by plant workers properly. Employing a formed precast concrete block offers several potential benefits over onsite casting.
Precast concrete production will be performed on the ground level, which helps with safety throughout the construction project. There’s larger management over material quality and craft in a very formed plant compared to a construction website. The forms employed in a formed plant will be reused tons of thousands of times before they need to get replaced, usually creating it cheaper than onsite precasting once looking at the price per unit of formwork.
What are the different types of Precast Concrete?
Check out the different types of Precast Concrete Walls:
1. Precast Beams
There are two main classes of beams that are used in precast building construction:
1.1 Internal beams – Wherever floor loading is approximately symmetrical
1.2. External beams – Wherever floor loading is predominantly-symmetrical.
2. Precast Floor Slabs
The main varieties of slabs are employed in the formed frames are:
2.1 Hollow cored block
2.2 Double tee block
3. Precast Walls
Precast concrete walls serve two functions:
3.1 Stability
3.2 As walls or boxes close staircases and carry shafts.
Walls are also classified as Infill or Cantilever
3.3 Infill walls consider contiguous composite action with the beam and column frame.
3.4 Cantilever walls or boxes act as deep beams to that the frame is hooked up.
4. Precast Staircases
Three choices are obtainable for formed staircases:
4.1 A single formed unit containing all the flights and landings
4.2 Separate formed flights and landings
4.3 Parts of the flights and landings are created in one piece.
5. Precast Columns
For structures of 5 stories or less, every column can commonly be continuous to the total height of the building. For precast concrete construction larger than five stories, two or a lot of columns are spliced along.
The main varieties of formed columns are:
5.1 Edge Columns –Symmetrical in one direction.
5.2 Internal Columns – Symmetrical altogether directions.
5.3 Corner Columns – Not symmetrical in the least.
Major Advantages of Precast Concrete Structures
Some of the major benefits of making precast concrete building are-
1. Thermal Insulation
All elements used here are of a well-engineered structural precast panel work put together, which provides a high insulation level in the building. Manufacturers generally use a combination of concrete and EPS foam to increase insulation capabilities.
2. Long Term Viability
Not only is precast concrete strong, but it’s also had a long life. Today, precast concrete structure is designed to last up to 100 years, which assures us that there will be no damage from elements, such as fires, animals, and natural disasters. No remodeling or replacing is required.
3. Aestically Pleasing
Long gone are days where boring concretes were being used. There are myriad varieties of precast available in the market. Any shape, size, and color are available. Precast materials such as granite, brick, and stones can also be-cast reducing the time and cost of installation. With little design specifics and creativity, you can get the design you want/ desire with better durability and stability.
4. Quick Installation
Speed is a critical element in the construction industry. With the help of precast panels, you can construct a larger completed footprint in a shorter amount of time. Precast panels can directly be installed in worksites without any delay.
5. Environment Friendly
With growing concerns about environmental waste, with precast concrete, that issue is resolved. Precast concrete is completely reusable and recyclable. This makes it an environmentally friendly choice because there is less wastage of materials, and it does not harm the environment in any way.